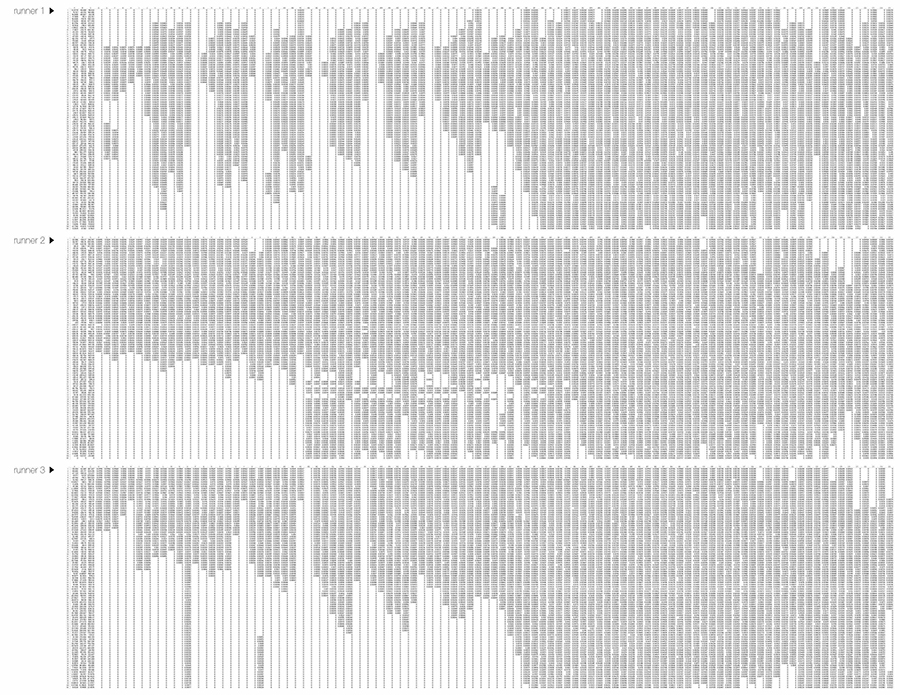
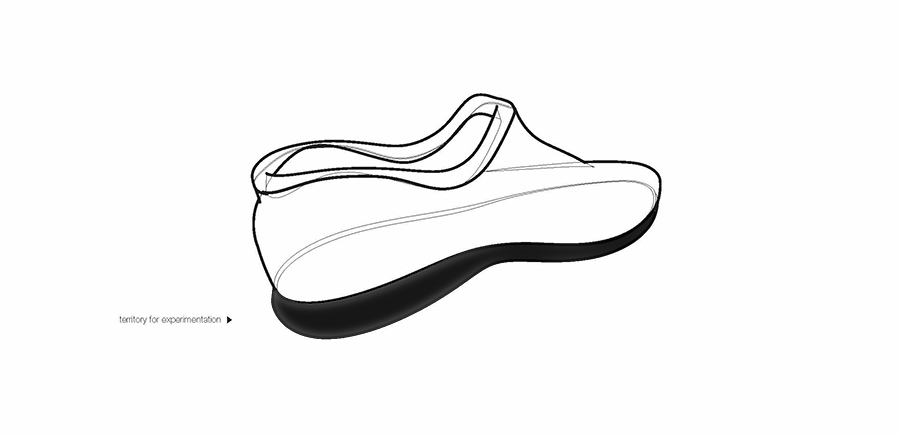
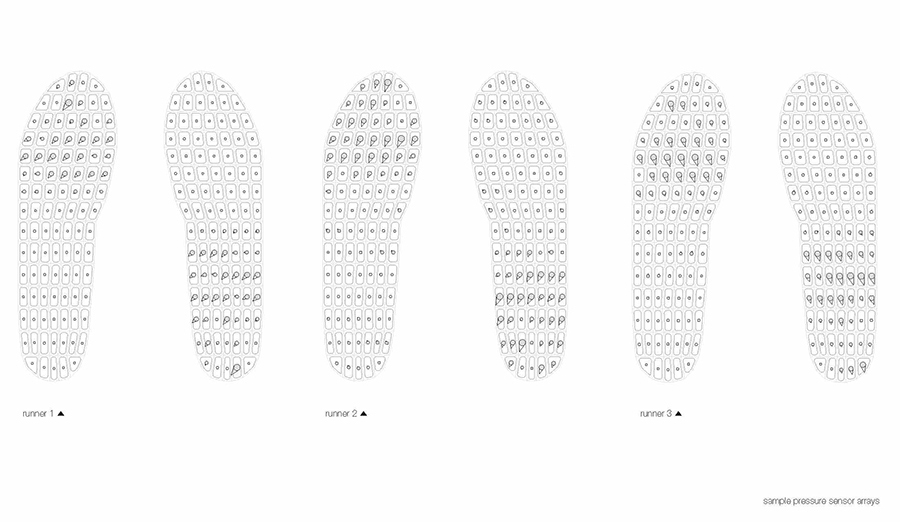
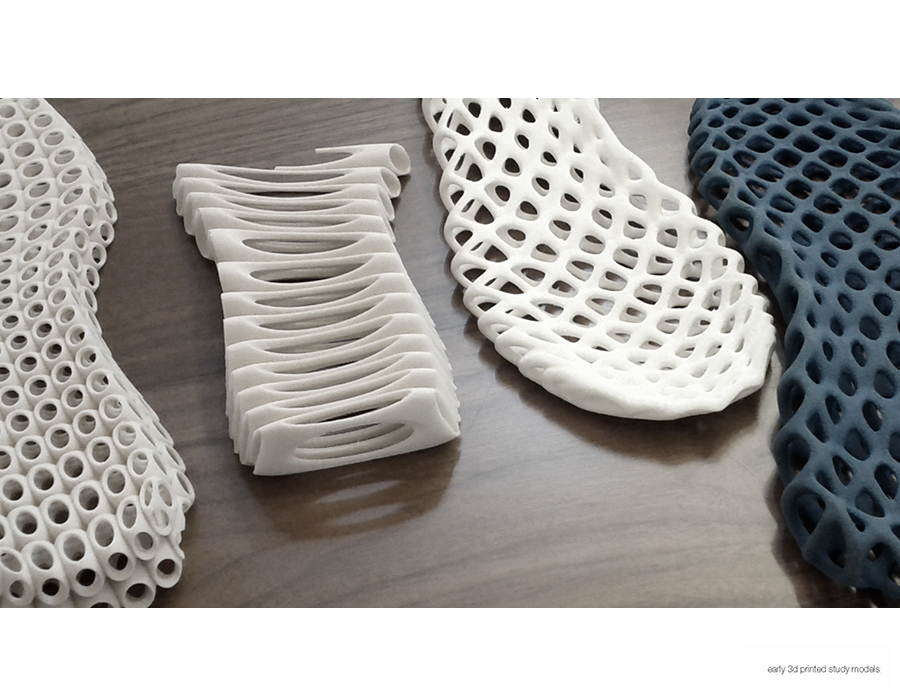
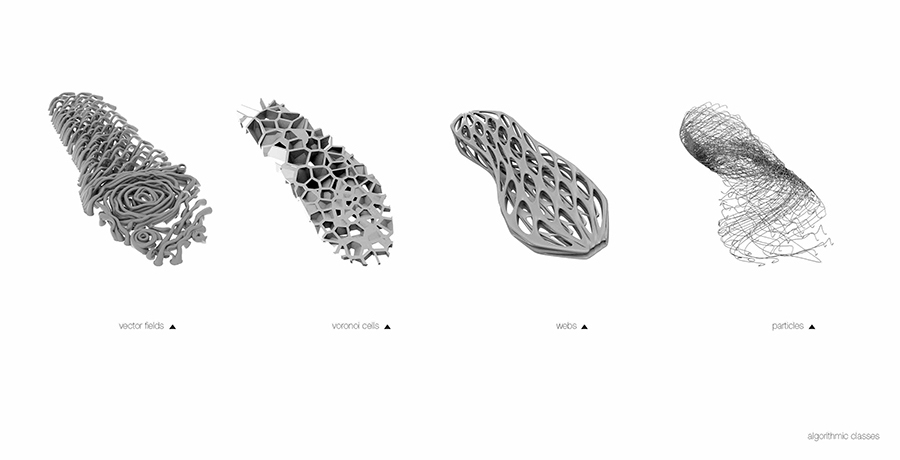
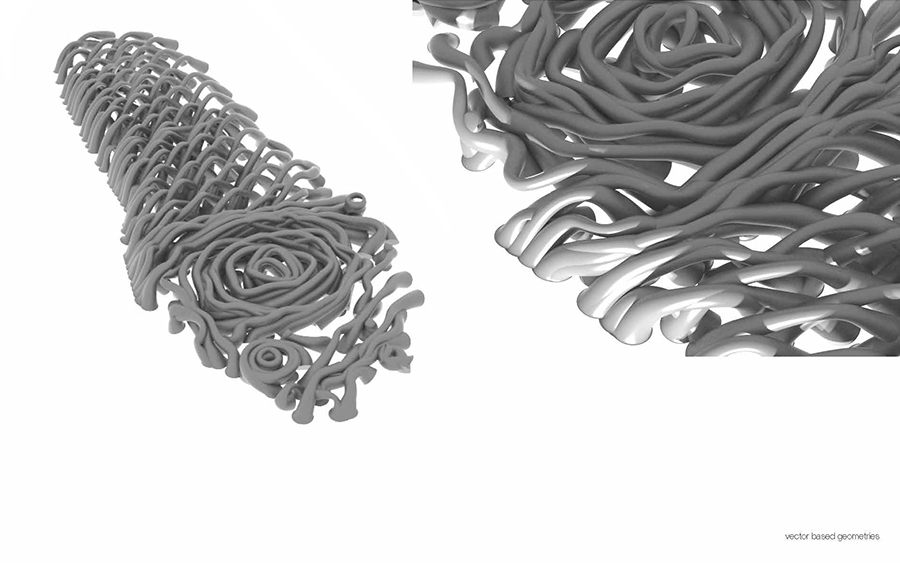
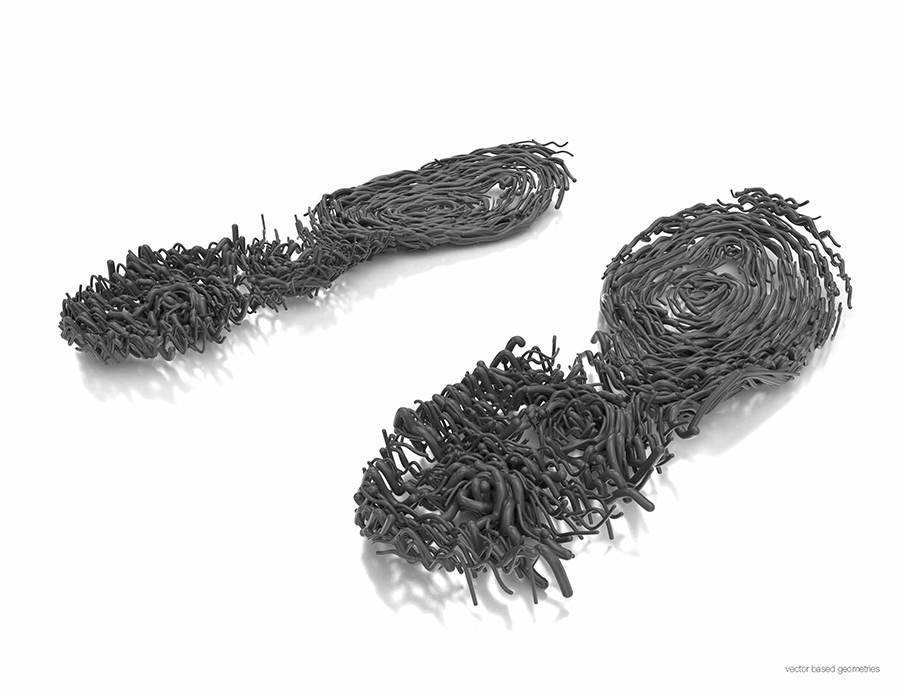
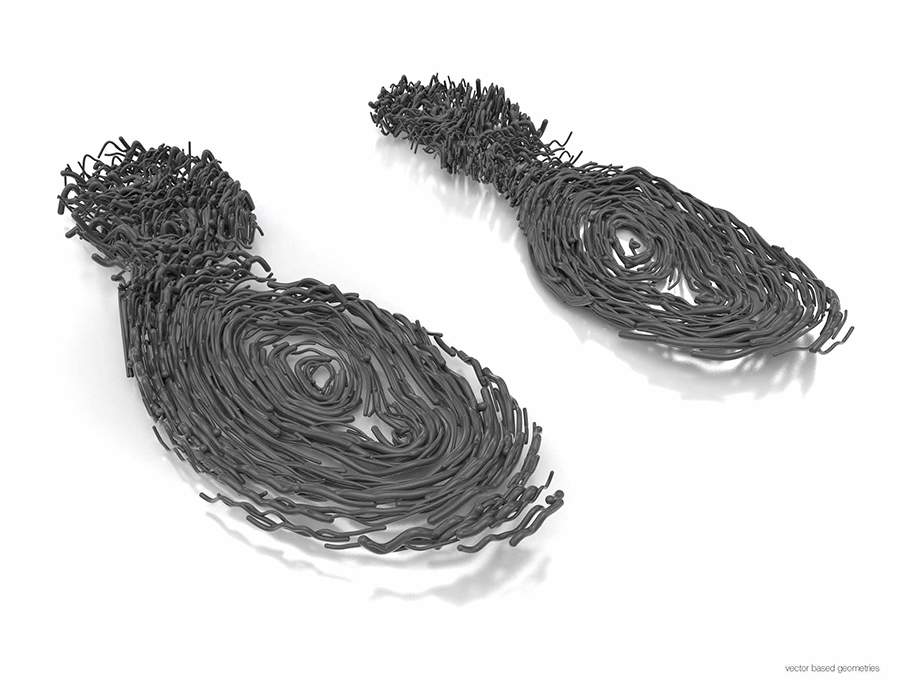
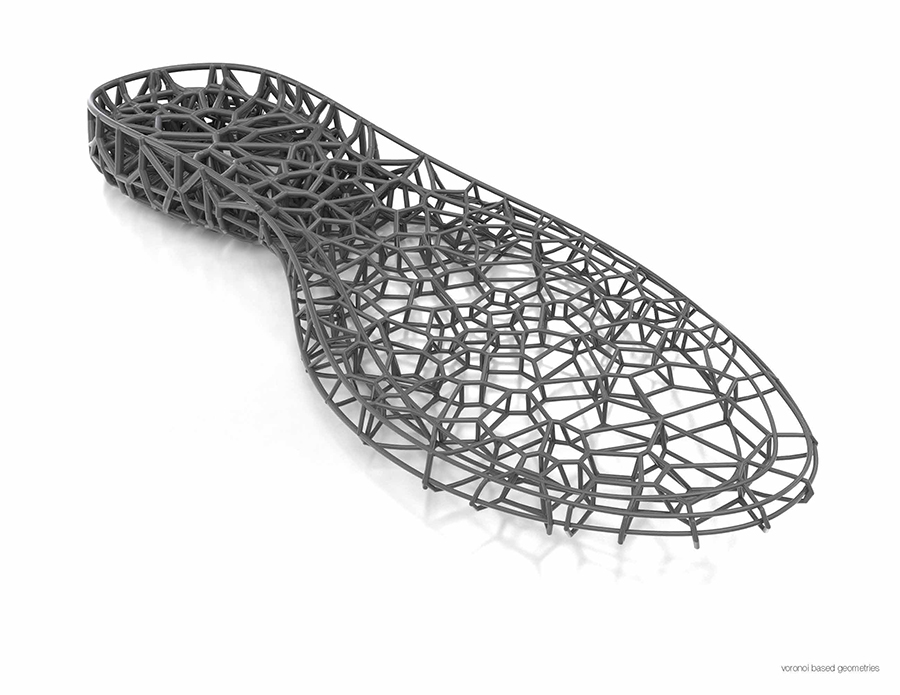
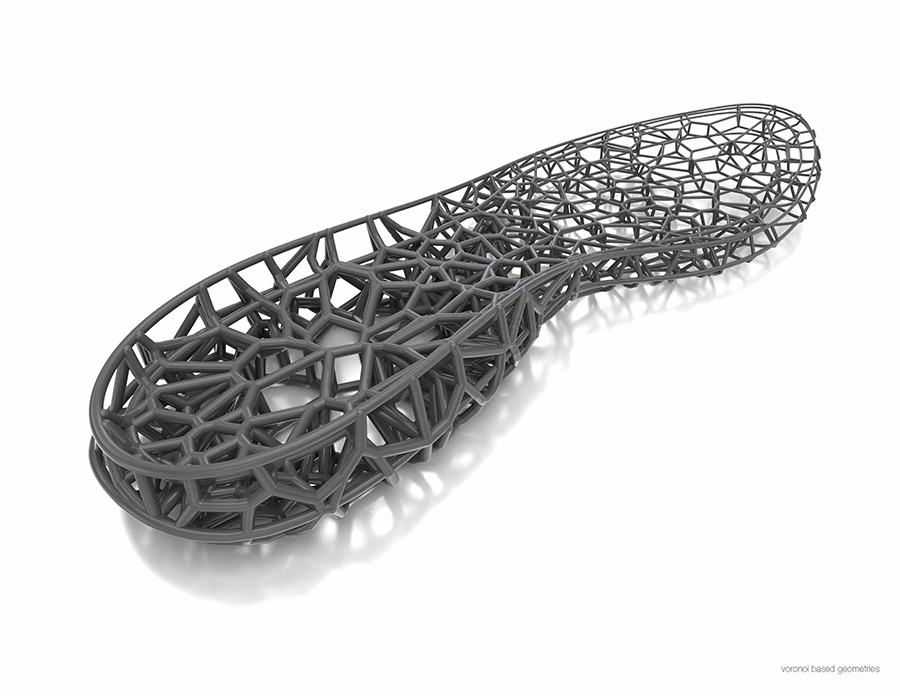
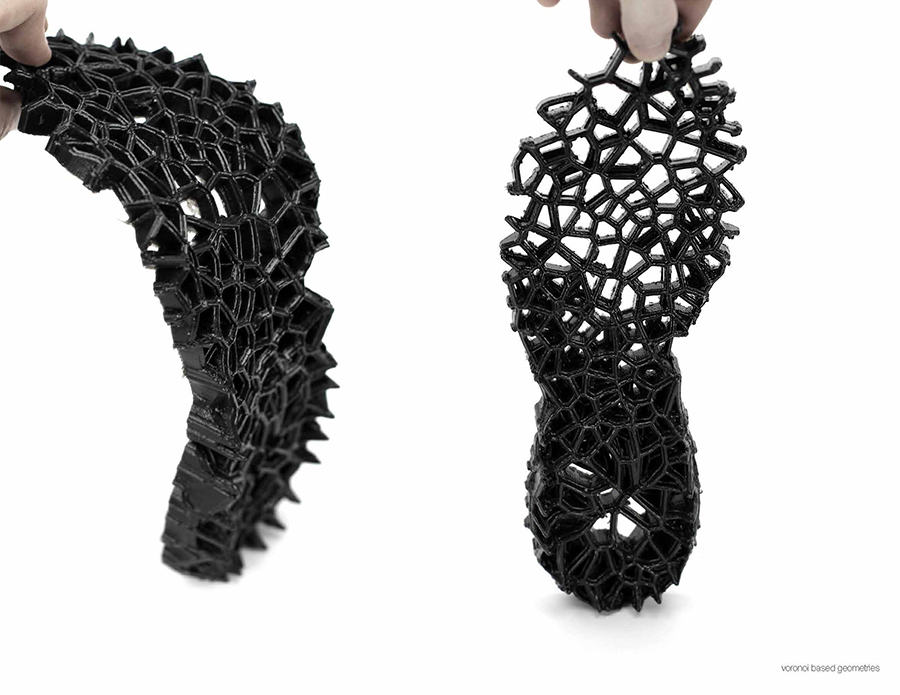
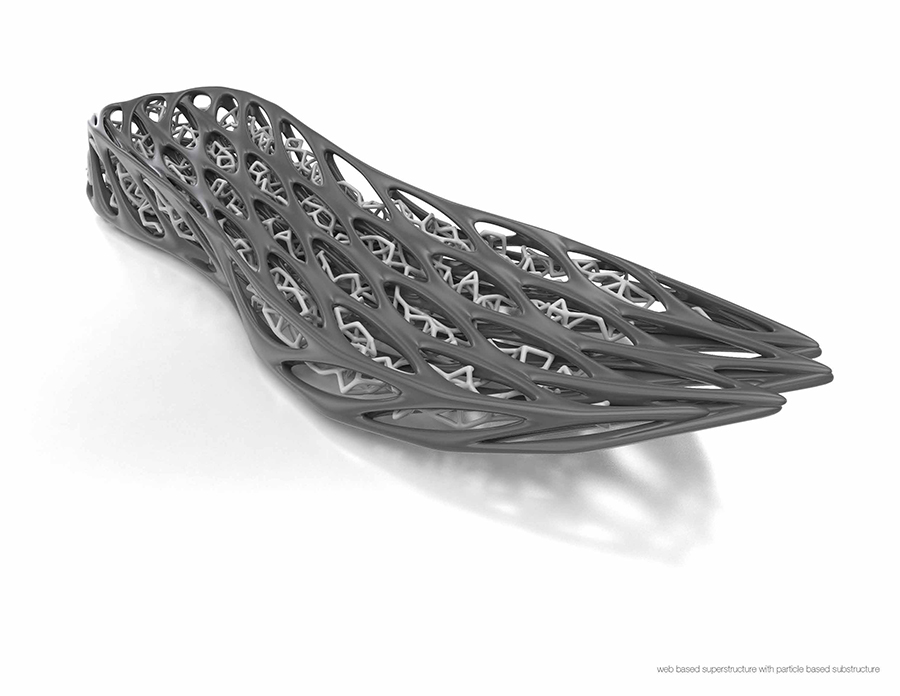
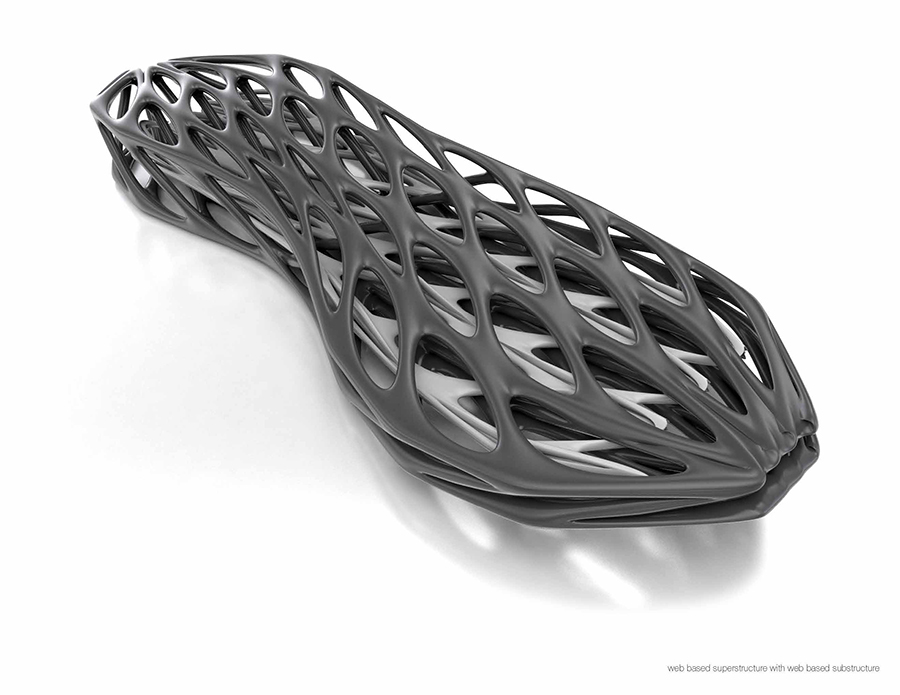
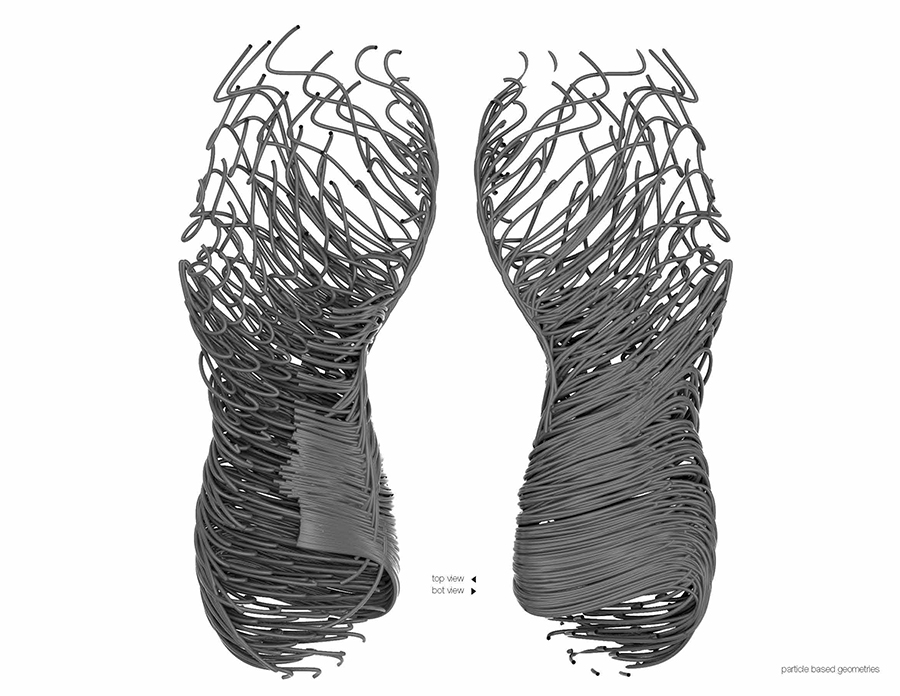
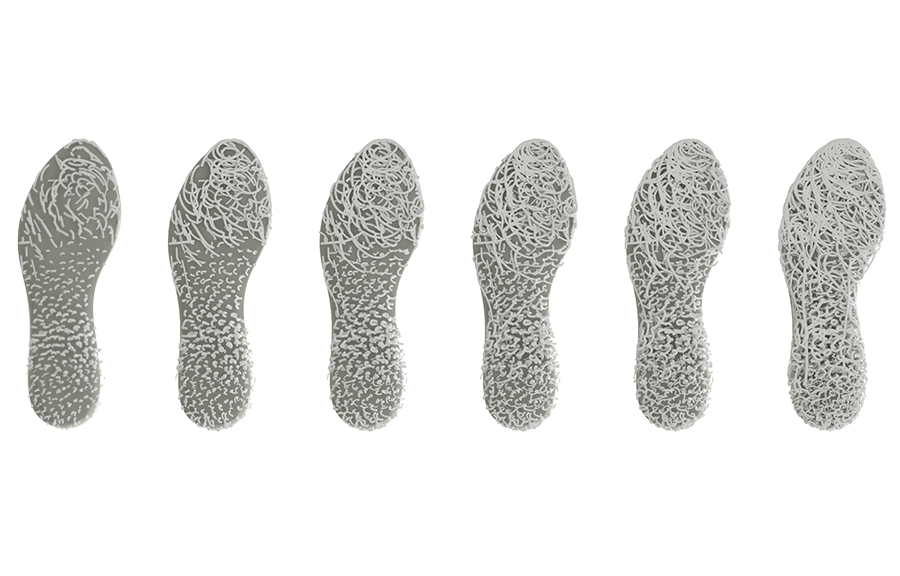
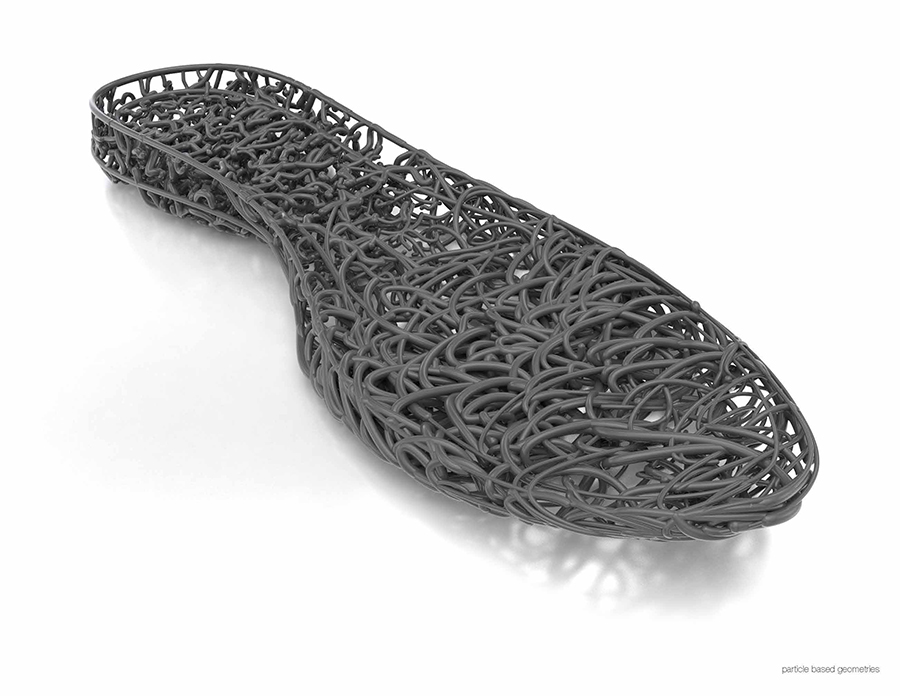
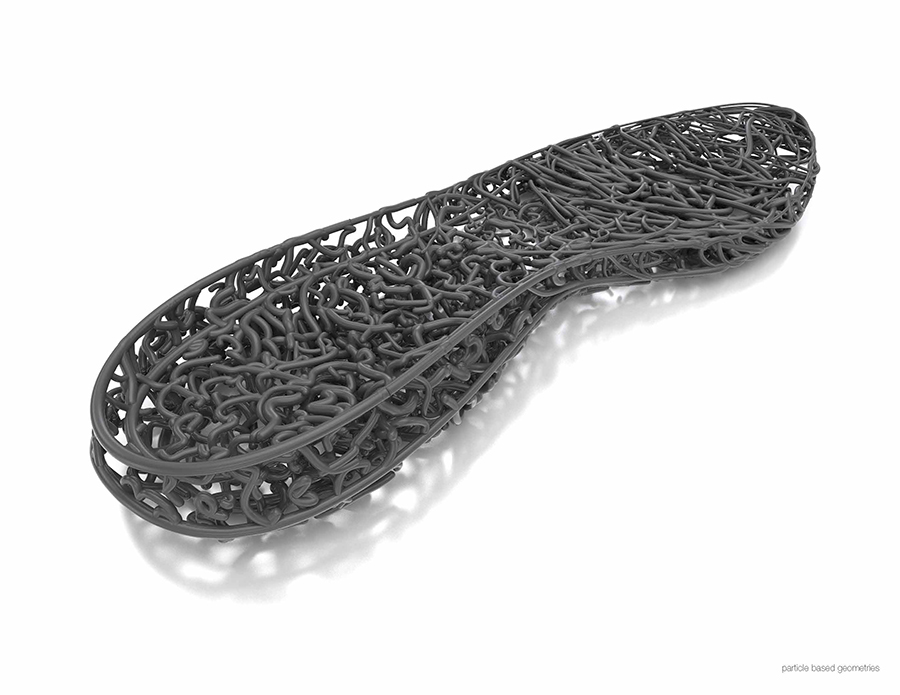
Generative Midsoles
New Balance approached Radlab with an interest in adding a new process to their running shoe manufacturing repertoire. Injection molding the various plastic parts that contributed to making a running shoe came with particular limitations that 3d printing could potentially overcome, namely, short run production cycles. In other words, if New Balance had an interest in making just fifty pairs of high performance running shoes for a particular user group, the price points of producing molds were often cost prohibitive. With the prospect of being able to make mold-less parts that could be specifically tuned to an individual runners stride, 3d printing technology offered clear opportunities.
In collaboration with New Balance’s Running Innovation Studio and Sports Research Lab, Radlab led the design research process of investigating data translation methods that would meet a series of challenges. At this time the Sports Research Lab had already been working with a number of runners to examine their running styles through the lens of their foot-stride. Rather than simply looking at total force applied per foot-stride, the Lab used a force plate with an essentially rectangular array of 100 pressure sensors, distributed across the runner’s sole. This enabled multiple points of force to be captured simultaneously, across the spectrum of a runner’s initial heal strike to the forefoot lift of both feet.
The pressure sensors rapidly collect and archive data cycles which are each only fractions of a second, documenting quantity and direction of force at the location of each sensor. The primary challenge was to use these large data sets from a particular runner’s gait as maps for generating a range of runner-specific midsole geometry solutions. The new sole structure needed to be light, with a relatively low material density, and composed in a manner that could be assembled to a soft upper. The intention for the midsole was a cored out, foam-like geometry, with rubber traction elements that would be post applied to the material as an outsole, the interface between the ground and the midsole. New Balance provided basic midsole dimensions, a 3d file containing foot form data, and basic functional attribute zones. Performance factors were the key drivers for structure and form.
The focus of our work was computational in nature, wherein our endeavor was to provide original conceptual and algorithmic frameworks from which New Balance could advance the work according to their particular needs and interests. Reading Microsoft Excel files into Grasshopper was a key factor in data management, enabling us to access and translate discrete amounts of data while testing and iterating. Each Excel file represented either the left or right foot of a runner, where the columns (x axis) represent time and the rows (y axis) represent each of the 100 pressure sensor readings. Four strands of computational inquiry were pursued in an effort to explore a range of possible solutions: vector fields, voronoi cells, webs, and particles. In some cases, opportunities for creating hybrid strands were explored. The potential of variable durometer 3d printing influenced one such trajectory, wherein the notion of a relatively high durometer substructure would act as selective/local reinforcement for a relatively low durometer super-structure. While each strand was explored using the same base data sets, the data was uniquely scaled, averaged, or otherwise numerically modified in order to filter out anomalous data points and discover compelling structural and formal configurations.
Status: Completed, 2012
Client: New Balance
Location: Lawrence, MA
Project Team
Matt Trimble
Esko Heilner
George Kontalonis