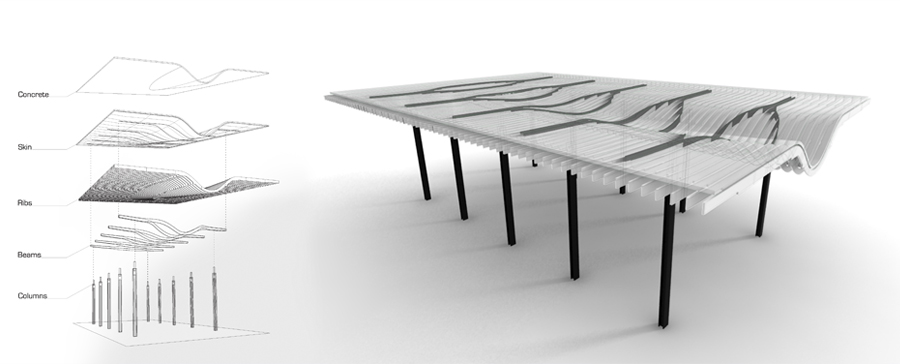
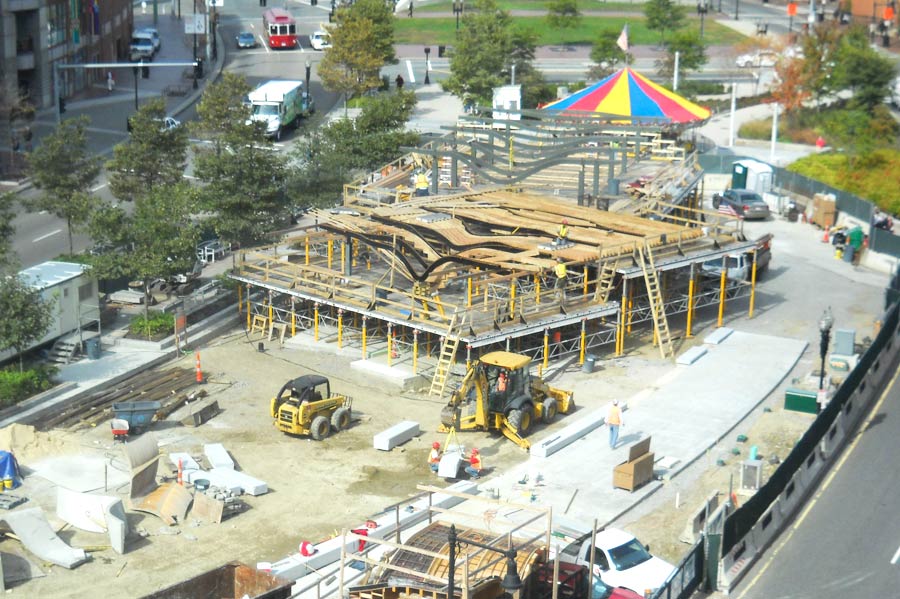
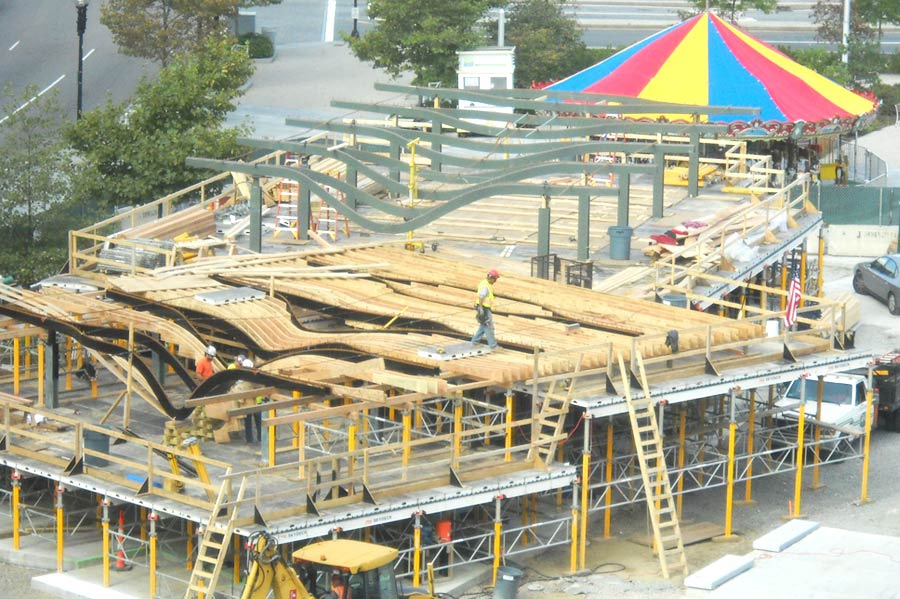
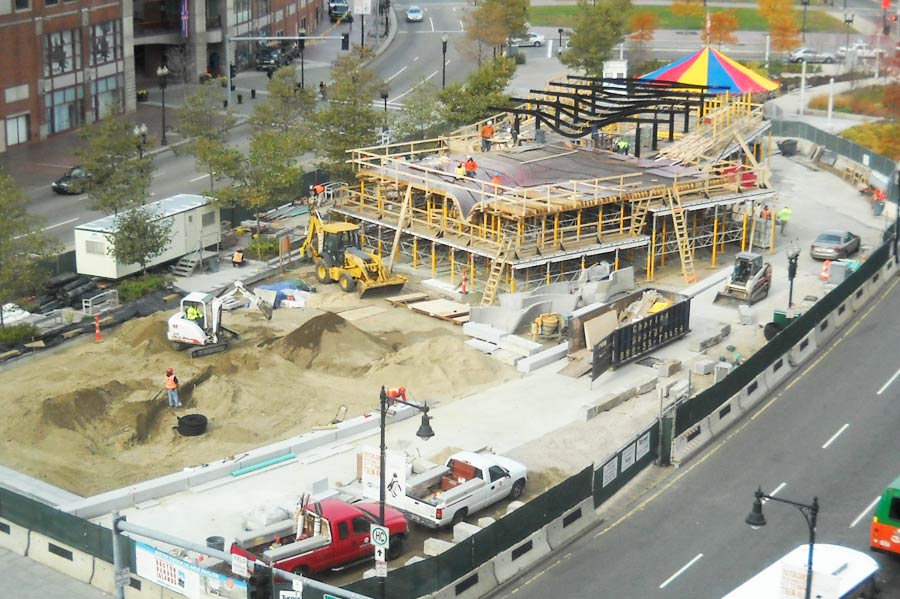
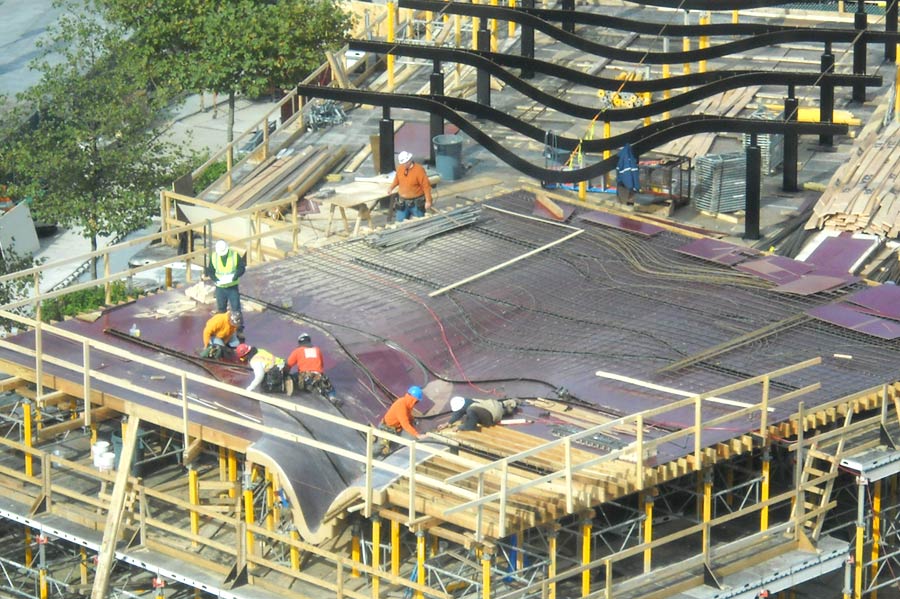
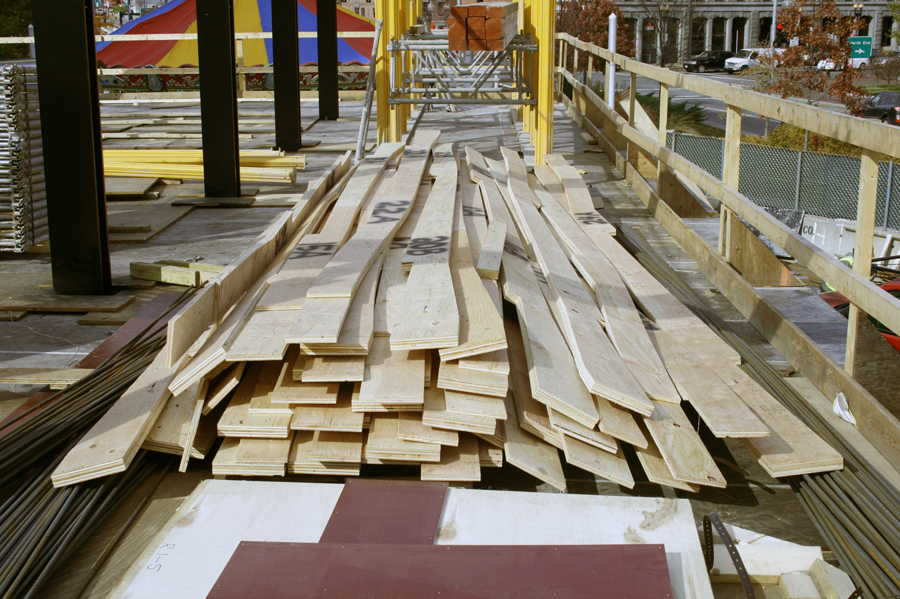
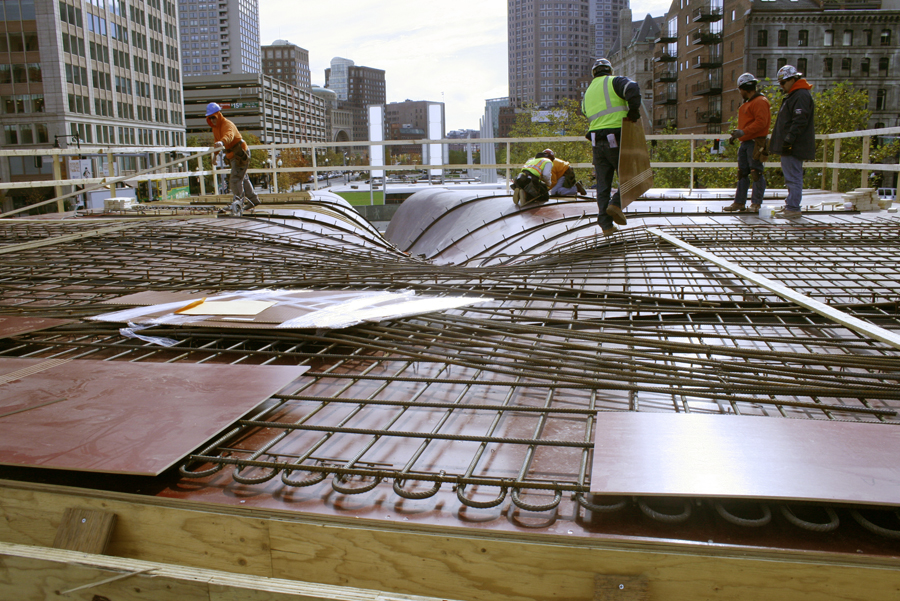
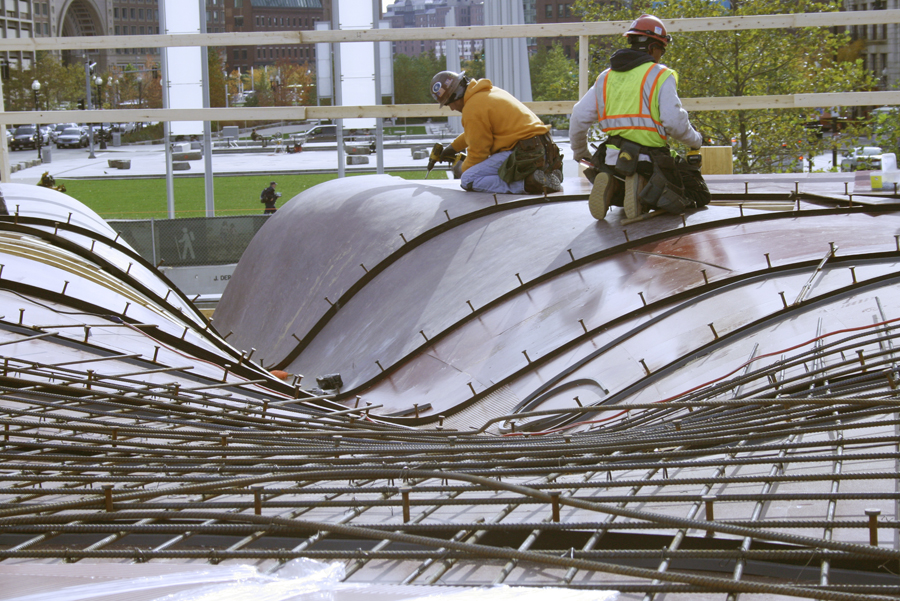

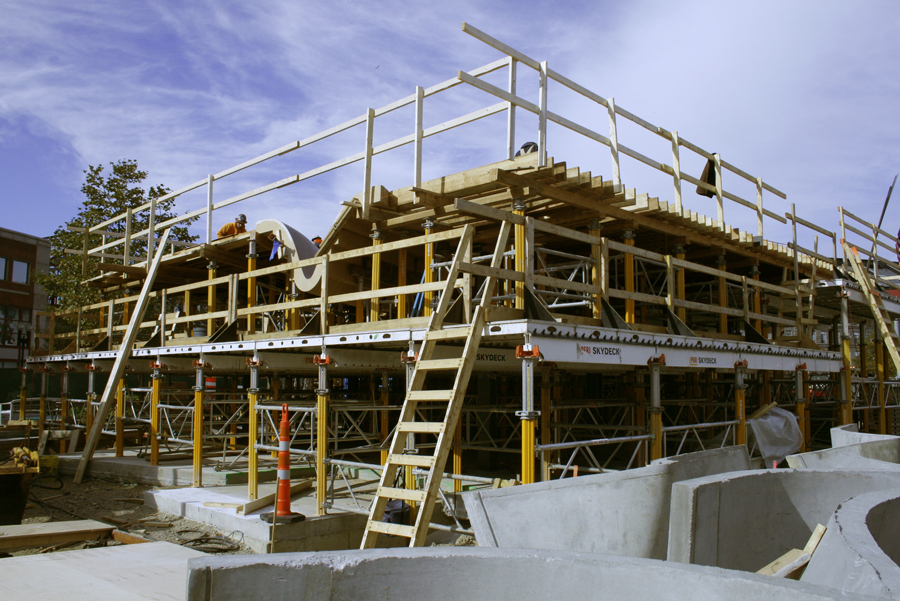
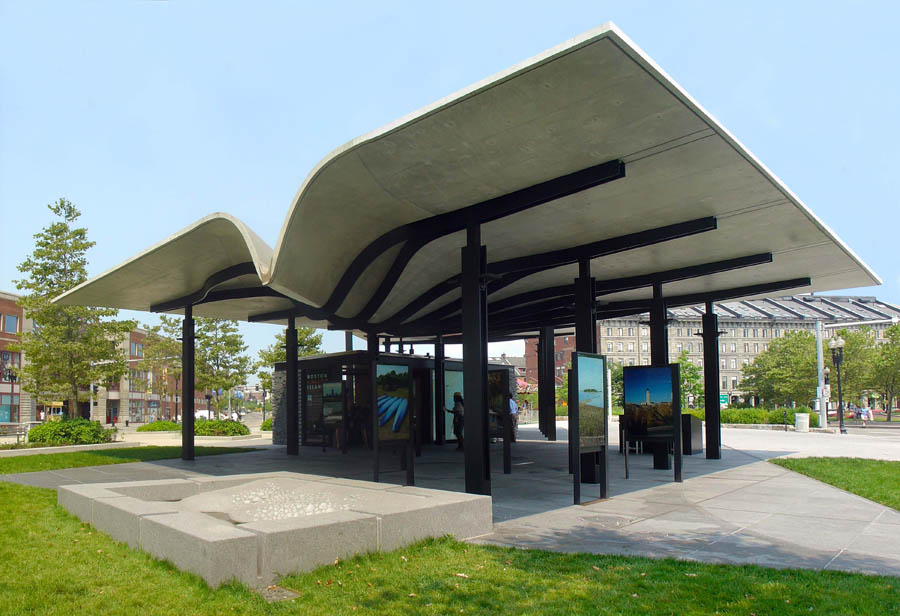
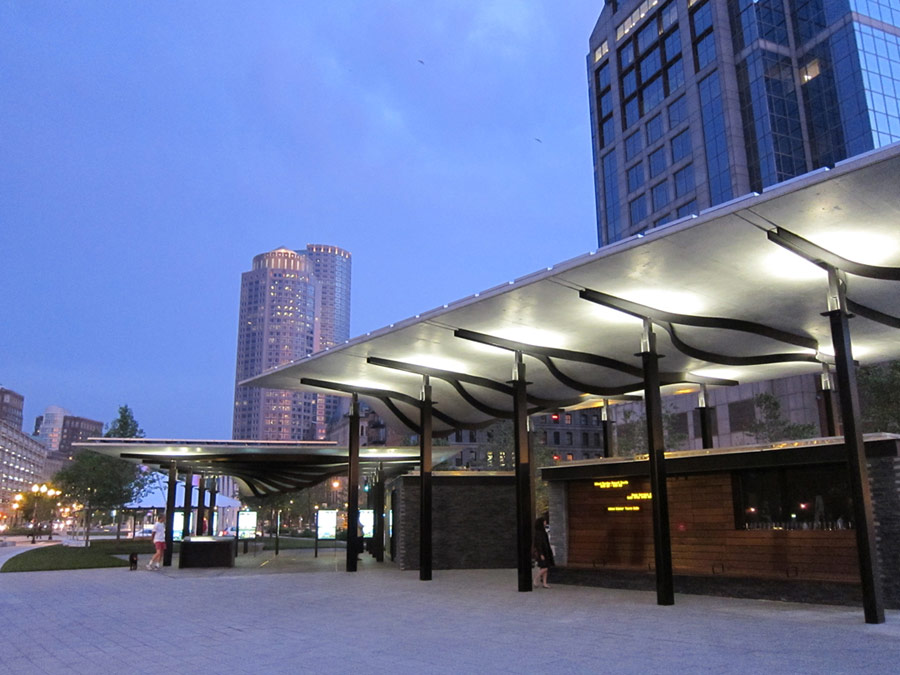
Boston Harbor Islands Pavilion
As the fabricators hired to create the formwork for the pavilion roofs, C.W. Keller and Associates invited Radlab to serve as digital fabrication consultants. Radlab enabled, with the provision of a series of scripts , the automation of rationalizing doubly-curved surfaces for CNC milling. The project encompassed two parts: developing a parametric method of creating the ribs used to support the concrete form work, and preparing a method for ‘unrolling’ hundreds of 3d surface formwork panels into 2d surfaces to be cut from flat sheets for CNC milling. Radlab began by establishing the fabrication constraints, construction parameters and assembly requirements. This part of the process was executed while pseudocoding the algorithms necessary for automating the otherwise repetitious tasks at hand. For the ribs, the code that was written transforms two compound curved surfaces that defined the top and bottom shape of the ribs into CNC-ready parts, nested and labeled according to their location. For the formwork panels, the code takes each individual 3d part, flattens it, labels and orients it, and adds screw holes based on rib locations for installation.
Photographs 1-4 provided by Turner Construction
Status: Completed, 2010
Client: C.W. Keller & Associates
Location: Boston, MA
Press
http://newyork.construction.com/new_york_construction_projects/2012/1112-island-gateway-aims-to-pique-tourist-interest.asp
http://blogs.bostonmagazine.com/boston_daily/2011/07/07/park-it-getting-to-the-harbor-islands/
http://www.unionparkpress.com/boston-harbor-islands-pavilion-grand-opening/
http://inhabitat.com/digitally-fabricated-boston-harbor-islands-pavilion-collects-rainwater-for-irrigation/
Project Team
Matt Trimble
Garett Hwang